Pii Center for Pharmaceutical Technology
We conduct interdisciplinary drug and polymer research that provides end-stage pharmaceutical products directed at therapeutic conditions, vaccines, antidotes and wound care.
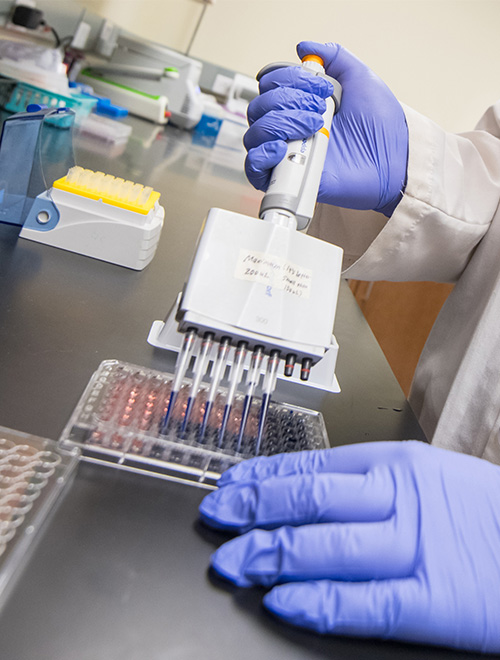
Welcome!
The Pii Center conducts interdisciplinary drug and polymer research that provides end-stage pharmaceutical products directed at therapeutic conditions, vaccines, antidotes and wound care. Utilizing cutting edge thermal processing, the Pii Center collaborates with private industry, government and academia to develop new, improved and expanded drug delivery systems.
The Pii Center for Pharmaceutical Technology (Pii Center) interfaces with the Department of Pharmaceutics and Drug Delivery at the University of Mississippi School of Pharmacy. The Pii Center is housed under the Research Institute of Pharmaceutical Sciences and provides a unique, multidisciplinary approach for enhancing the development, characterization and production of pharmaceutical dosage forms.
Our Mission
The Pii Center for Pharmaceutical Technology (Pii Center), a unit organized under the Research Institute for Pharmaceutical Sciences (RIPS), conducts interdisciplinary drug/polymer research that provides end-stage pharmaceutical products directed at therapeutic conditions, vaccines, antidotes and wound care.
This unique center leverages the existing expertise and resources at the University of Mississippi (UM). Utilizing cutting edge thermal processing, the Pii Center collaborates with private industry, government and academia to develop new, improved and expanded drug delivery systems.
Many drugs and biological products require special delivery systems. The Pii Center provides problem-solving approaches for the development of cost-effective, patient friendly and efficacious delivery systems for existing active pharmaceutical ingredients as well as for new chemical entities. Utilizing solid solutions and dispersions and nanotechnology, the Pii Center develops novel formulations to improve bioavailability and therapeutic efficacy.
UM’s patented ‘Hot-melt Extruded Laminated Platform’ (iHELP™) technology, for example, promises broad-based availability of essential medicines for rapid response to both civilian and military personnel. Additionally, the Pii Center focuses on industrial pharmacy, developing Process Analytical Tools (PAT) and other methodologies to incorporate Quality by Design (QbD) principles and therefore increase the end-product success rate.
Pharmaceutics International, Inc.
Pharmaceutics International, Inc. (Pii) is a privately held drug delivery solutions company providing dosage form development and GMP Manufacturing services to the global pharmaceutical industry. Pii’s vision is to become the benchmark in pharmaceutical product development outsourcing. Headquartered in Hunt Valley Maryland USA with European development and manufacturing facilities in the UK, Pii offers preformulation testing, formulation development and clinical trial material and commercial manufacture of parenteral, solid, semi-solid and liquid dosage forms.
Campus Partners
Office for Research and Economic Development
The Office for Research and Economic Development (ORED) at the University of Mississippi empowers research that advances knowledge, addresses social challenges, and propels economic growth locally and nationally. Our role is to support researchers, foster collaboration, and facilitate the translation of innovation into progress.
-
Hands-On Course in Tablet Technology
The Hands-on Course in Tablet Technology is a post-graduate educational program offered by the Pii Center for Pharmaceutical Technology that provides an extensive review of conventional and advanced manufacturing technologies, including hot-melt extrusion, that is used to develop a variety of novel delivery and continuous manufacturing systems. The course, initiated in 1998, has trained over 2,000 attendees.
Learn More
Hot-Melt Extrusion
Hot-melt extrusion (HME) technology has been a widely used manufacturing process in the plastics industry for more than half of a century and has recently been demonstrated to be a “continuous process” for the pharmaceutical industry. Over the last two decades, pharma has gradually focused on HME techniques for many drug delivery applications, which is evident from the scientific literature. In the last 15 years, over 200 research papers and many several reviews have been published on the subject. In addition, HME patents issued world-wide for pharmaceutical systems have increased since the early 1980’s.
HME offers several advantages over traditional processing techniques for pharmaceutical applications. The process is anhydrous, entails a continuous operation necessitating fewer processing steps, entails no organic solvents, requires no compression of the actives, and improves bioavailability due to dispersion of the drug at the molecular level in the final dosage forms. All of the components in the formulation must be thermally stable at the processing temperatures utilized, which may limit the extrusion of thermosensitive actives. However, advent of new techniques such as a combination of HME with nanotechnology, powder coating and complexation over the last several years continuously adds active pharmaceutical ingredients (APIs) to the HME list of candidates. Advancements in types of extruders have also expanded the number of drugs available for processing. For example, twin-screw extruders with flexible screw designs and inclusion of injection ports at different stages within the barrel permit the pharmaceutical scientist more freedom in the development of intricate dosage forms.
The extrusion process involves conversion of the API and excipients into a product of uniform shape (such as a fast-dissolving film or tablet) and density by forcing these materials through a die under controlled conditions. In HME, the meltable substances may be polymeric materials or low melting point waxes. Hot-melt extruded films may be produced separately and layered post-extrusion, or a multi-layered system may be co-extruded. In addition, pellets, tablets and capsules may be produced with this continuous process. The bioavailability of the drug substance for oral and other delivery routes may be improved when it is dispersed at the molecular level in HME dosage forms. New chemical entities, isolated natural compounds, and currently marketed drugs that demonstrate a low bioavailability due to solubility issues are prime candidates for this technology. Thus, hot-melt produced dosage forms present the pharmaceutical scientist with new opportunities, including the attainment of zero-order drug release when desired.